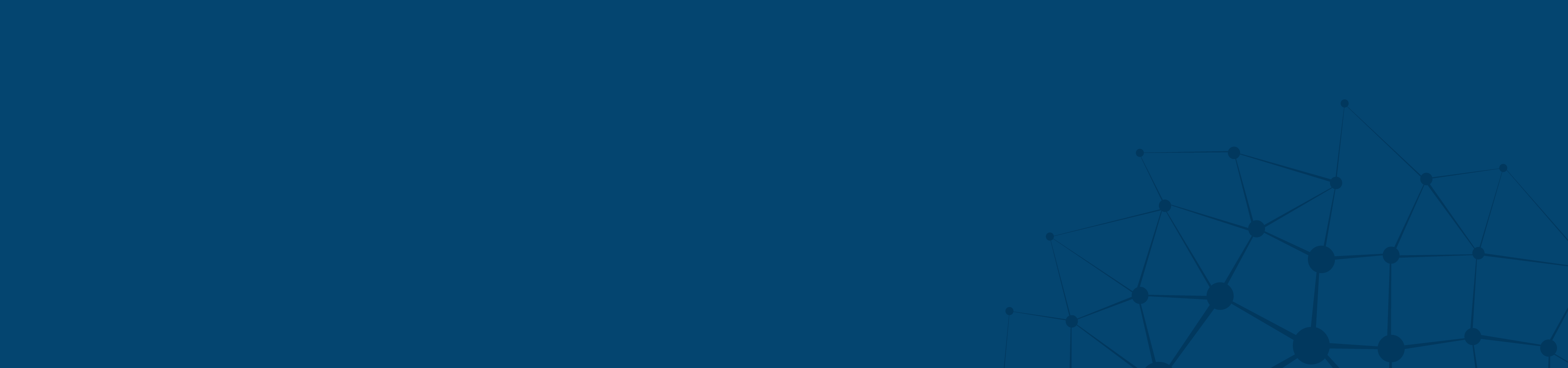
ICD laat robots samenwerken met mens én fabriek
Nieuws | 5 november 2019

De huidige smart industry kent vooral low-volume, high-mix, high-complexity productie die vraagt om flexibele en intelligente automatisering. Daarvoor is een robot nodig, die veilig kan samenwerken met mensen, snel is om te stellen en compleet geïntegreerd is in de besturing van het productieproces. Dat is de connected collaborative robot, kortweg cobot. Innovatiecluster Drachten (ICD) zette er in 2017 een CCR-project voor op.
Diverse bedrijven verkenden de toepassingen van cobots en AIV’s (autonomous intelligent vehicles die op de werkvloer tussen de medewerkers door navigeren en dus eigenlijk ook een soort cobots zijn). Begin dit jaar startte het vervolgproject, CCR 2.0. Daarin werken zes ICD-leden (BD, Neopost, Photonis, Resato, Variass en Ventura) samen met twee noordelijke hogescholen (Hanze en NHL Stenden).
Veiligheid voorop
Het doel is tweeledig, vertelt Joost Krebbekx, programmamanager van ICD. ‘We willen uiteenlopende processen gaan ‘cobotiseren’, waarbij het veilig samenwerken met mensen voorop staat. Je ziet cobots al veel toegepast worden voor pick & place-taken, maar wij trekken het breder naar processen als solderen, schroeven, kitten en assembleren. Ik denk dat we daarmee als Noord-Nederland vooroplopen. Daarnaast kijkt een van de bedrijven ook naar de toepassing van cobots in zijn eindproducten. Ten tweede willen we de cobots verbinden met de besturing van de fabriek.’
Omstellen
Een enthousiaste CCR-deelnemer is Variass, een system supplier en EMS-specialist (electronic manufacturing services) die elektronische en mechatronische oplossingen ontwikkelt en produceert in Veendam en Drachten. Het bedrijf zet cobots onder meer al in voor het solderen bij de assemblage van elektronica, vertelt Jan Betten, hoofd Variass Development Support (VDE). ‘In CCR 1.0 hebben we geleerd hoe we de cobot als onderdeel van de fabriek kunnen laten fungeren en hoe we dat veilig houden. En we hebben de businesscase leren begrijpen. We gaan langzaam toe naar de productie van unieke producten, single-piece flow, en dat betekent dat we vaak moeten omstellen. Bij traditionele industriële robots kost dat veel tijd. Wij willen die omsteltijd reduceren, het omstellen door lager geschoold personeel kunnen laten uitvoeren en – het ultieme doel – een robot zichzelf laten omstellen. Voor de assemblage van elektronica betekent dit bijvoorbeeld dat de robot zichzelf kan inleren op verschíllende printplaten en de soldeerverbindingen die hij daarop moet maken.’ De insteek van CCR 2.0 is voor Variass dan ook dat de robot connected moet zijn met de fabriek. Hij moet CAD-/CAM-tekeningen kunnen lezen en verbonden zijn met het ERP- en het MES-systeem. ‘Vanuit ERP ontvangt de robot zijn werkinstructies en in MES kunnen wij de status uitlezen van orders die de robot uitvoert en de bezetting van de robot.’
Waardering
In het CCR-project waardeert Jan Betten de samenwerking met de ICD-partners vooral omdat zij met geheel andere processen bezig zijn en soms al veel ervaring met robots hebben. Bovendien kijken zij op een andere manier naar bepaalde zaken. ‘Als deelnemende bedrijven organiseren we bijeenkomsten waar we kennis uitwisselen over complexe onderwerpen, zoals grippers, vision, deep learning, et cetera. Samen krijgen we ook makkelijker toegang tot kennisinstellingen en leveranciers, die graag aan meerdere bedrijven tegelijk presentaties willen geven. De hogescholen zijn goed in robot- en sensortechnologie en vision.’
De hogescholen brengen hun expertise in, maar in CCR zijn het toch vooral de bedrijven die van elkaar leren, beaamt Krebbekx. ‘Begin volgend jaar gaan we ervaringen uitwisselen met bedrijven op Brainport Industries Campus in Eindhoven.’
Dit artikel is gepubliceerd in LINK Magazine van oktober 2019