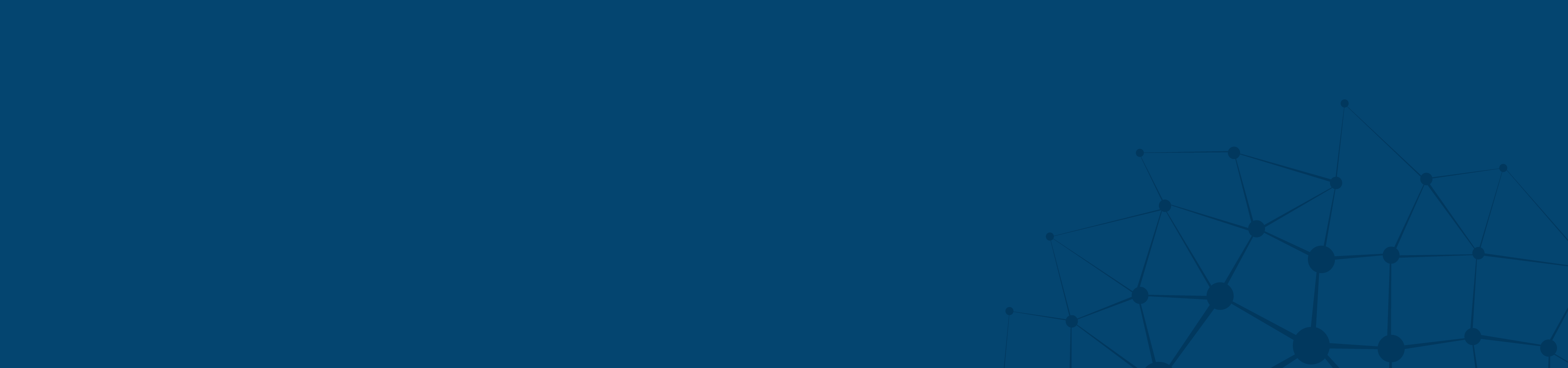
'We make the impossible possible'
News | 20 January 2016

Anyone looking for ultra-precise parts, components or systems 'on the edge of technology' will come to NORMA in Drachten. The former Philips toolmaker is the worldwide preferred supplier to the high-tech industry and one of the few companies that can guarantee an accuracy of (less than) one thousandth of a millimeter.
By Berend Henk Huizing
Proton irradiation is a new radiation technique to treat cancer. Doctors can deliver radiation at depth with a special pencil beam and thus treat a tumor in a very targeted way. Due to this technique, hardly any radiation is released to tissues other than the tumor, so that healthy tissue can be better spared. This form of radiation is not yet given in the Netherlands, but it is in Germany and Switzerland. ,,We make some of the most critical parts for the manufacturer of these irradiators'', explains Lars de Groot, plant manager at Norma Drachten. “We don't need to know anything about how the device works, we need to know what the function that the device performs can best look like. That is why we work closely with our clients. We only provide tailor-made solutions and cooperation with the client is essential for this.”
"Many techies really think it's a candy jar here."
Norma is a high-tech frontline supplier that makes highly accurate parts from paperclip sizes to shoebox size. Moreover, these parts are made of different materials such as stainless steel, aluminum and the exotic materials Molybdenum and Tantalum. Examples include tools for shaver caps at Philips and machine parts and assemblies for chip production at ASML. The high-tech company is one of the few in the world that can guarantee an accuracy of less than one thousandth of a millimeter. ,,Our main markets are defense, optical and consumer components and the medical industry. They all need precision parts for components where there is often only one of them. In addition, our customers demand a very high delivery reliability, which we can guarantee. The letters of our name do not stand for Nie Ohne Richtiges Messen Arbeiten for nothing. We know for sure what we are making, the quality of our products is the top priority.” Norma's customers must be able to rely 100 percent on what they receive is good and can be delivered for many years to come. “We are able to supply ten products per week for years. You have to be able to do both: help new customers with the best process and also provide the customer with the best parts for a long time.”
Moore
According to De Groot, Norma's strength lies in its extensive experience in the field of ultra-precision activities. “Where other suppliers stop, we continue, that's what we are known for. We do not sell 'no' and we always look for possible solutions together with customers. We try to make the impossible possible. That is part of our corporate culture.” Norma does not employ physicists who scientifically calculate all materials. ,,Our production employees are technically trained and because they follow experienced colleagues from the start and receive specific professional training, their learning curve is strong. This increases their level of knowledge and increases the quality and accuracy of our products. Moore's law almost applies to us. We are working more and more precisely: ten years ago we were at 10 µm, now it is 1 µm. The parts we make today are much more accurate and more difficult to manufacture than they were last year. And that is every year. This means that we continue to invest in our people and machines.” The fact that Norma is an attractive employer is apparent from the large number of applications for internships and open applications. ,,People come to work here because of the hardcore technology, on the border of the makeable, even though we don't make a recognizable product like a car. You work here with the best machines and have the freedom to operate them yourself. Many techies really think it's a candy jar here."
3D printing
To stay ahead, Norma has started a new adventure, 3D printing. The current technology that Norma uses removes material to make products. For example, consider milling metal. With 3D printing, the production method is exactly the other way around: building products little by little. “That requires a different way of working and therefore a different way of thinking. That is why we are participating in the 3D project of the Innovatiecluster Drachten.” The high-tech companies jointly purchase an industrial 3D printer. "Alone we could never have done this, but together we can put together enough money to buy one or two printers." Norma provides the knowledge of machines and their maintenance in this project. “For example, you have to think carefully about how to keep the machines clean, the timely replacement of wearing parts and the management burden of such a machine. Our knowledge and experience of how materials behave has proven to be very valuable.” As soon as the machines are available, the high-tech parts maker will test and try them out. “We need to learn how materials behave when they are built up rather than milled away. After all, the quality must be excellent so that our products remain reliable. These tests may show that certain materials are suitable and others are not.” Small series may already be produced within a few months, but De Groot does not expect to have its own 3D printers in production before two years' time. “So we want to know in time what can and cannot be done with it. It is expected that, due to the high-precision products we make, post-processing will always be necessary after 3D printing and that for some products, 3D printing takes too long or is too expensive, so that conventional machines remain usable.”
norma
In 1954 the Austrian Georg Blaim founded the company Norma in Hengelo, 'Nie Ohne Richtiges Messen Arbeiten'. Blaim was quirky, something that still characterizes the company today. In 2006 Norma missed out on a major assignment because it was said to be 'too small'. Partly for this reason, the management decides to continue to grow through acquisitions. In Hengelo, for example, the machine factory of electronics group Thales is taken over and in Drachten the machine factory from Philips. In May 2014, Norma takes over engineering firm Mecon. Norma Groep has 400 employees and four branches.