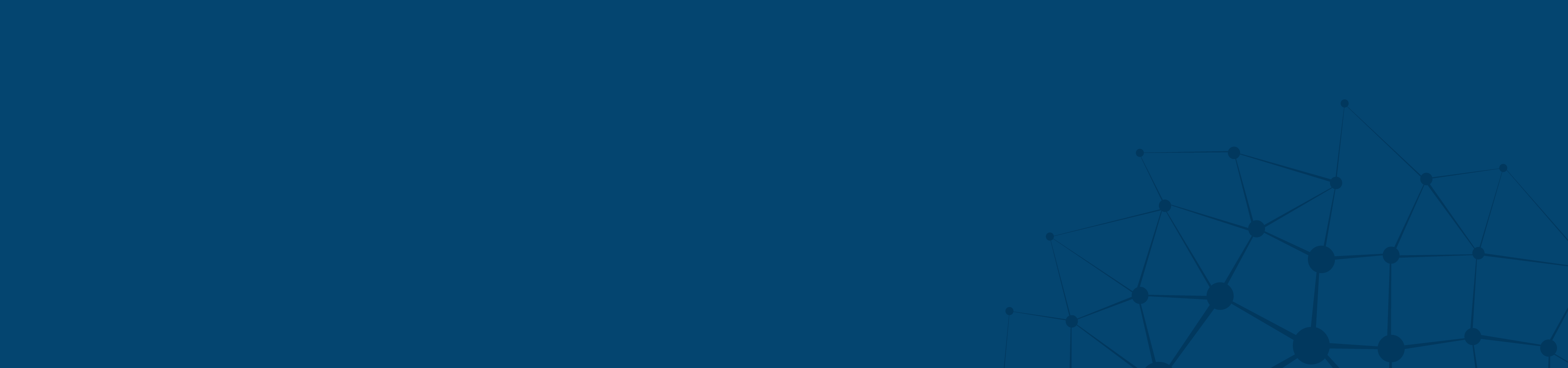
Together you achieve more
News | June 16, 2015

High-tech companies from the North joined forces in 2011 and formed the Innovatiecluster Drachten. The aim is to raise awareness of the area in and around Drachten as an innovative, technological and knowledge-intensive region. The results are not forthcoming. The companies exchange knowledge with each other, together they are more attractive to (scarce) technical personnel and share costs. The Additive Manufacturing (AM) project, better known as 3D printing, is a good example of this. Five companies of the innovation cluster – Philips, Neopost, Irmato, Norma and BD Kiestra – participate. What benefits does the partnership offer?
“Our company is involved in Electro Chemical Machining”, says Kees de Regt, System Architect at Irmato. “The nice thing about 3D printing is that you can immediately build the complex shape of ECM tools from a CAD file. In addition, with ECM technology, an even supply and distribution of the process fluid is essential. With AM, the necessary flow channels can be designed much better than is possible with existing manufacturing techniques.”
However, 3D printing in metal is not yet a piece of cake. It is more difficult than 3D printing in plastic. Kees de Regt: “Every company finds its own way. However, Irmato does not have sufficient clout and resources to develop this technology completely independently. The other companies in the innovation cluster have more in-house expertise. The innovation cluster has brought various parties together. Together you can achieve more than individually.”
Martin Pater, Innovation Manager Norma Groep, can confirm this: “Norma specializes in removing material. We are constantly looking for smart, new technologies that match our competencies, such as 3D printing. In doing so, you build up material and you don't have to cut (remove) as much. With the innovation cluster, we unite our strength with that of major players, such as Philips and Neopost. We are not competitors, but reinforce each other. Collaboration is an optimal form of knowledge sharing. The Netherlands is lagging behind in the field of 3D printing in metal; we can catch up with the innovation cluster.”
New chances
“Together you go further”, agrees Klaas Stuiver, Manager Tooling & Prototyping at Neopost. “The collaboration is also its strength. It offers a lot of potential to help each other to progress in this way. Where otherwise you often do not get any further and have to reinvent the wheel yourself, you can now quickly determine the right direction together within the cluster and expand from there. Moreover, as an innovation cluster you are a much more interesting partner for the suppliers of 3D printers. Together you can further develop the technology and exert influence.”
The ultimate goal of the project is to set up a 3-D 'shared facility' in Drachten. Here, companies can 3D print all kinds of parts and tools with metal. According to Klaas Stuiver, 3D printing with metal offers many opportunities and benefits for business. “You can build your first prototype and create sight models relatively quickly. You can also make parts that were previously impossible to produce. One of the many benefits that you can realize with Additive Manufacturing in metal is an enormous weight and material saving. You only have to print the contours, which creates hollow spaces. It also makes more sense to print organically shaped parts. Weight saving is an important topic for moving parts: the heavier parts are, the more power and effort it takes to accelerate and decelerate them.”
Creating compositions with integrated functions in one go is also an option. Klaas mentions a Bahco wrench as an example. It consists of five separate parts that are then assembled. “With Additive Machining you can print the entire key in the assembled state in one go, saving you a lot of time.”
In addition, it is now possible to produce a part without expensive tools and moulds. “Additive Machining is not a replacement for existing production techniques,” says Klaas, “but it is a good addition. In most cases you will continue to need the existing techniques in addition to creating via AM.
Surface finish is another issue. Because parts are built by fusing together very small powders, in a variation from 5 microns to a maximum of 60 microns, you can see this in the surface roughness.”
More efficiency
Lucas Boelen of Philips CL scouts for new emerging manufacturing technologies, such as 3D printing. Why does Philips use Additive Machining in metal? Lucas: “It is suitable for injection moulds, for example. With 3D printing you can create all kinds of curved cooling channels directly below the surface. As a result, a product cools down faster and you increase the efficiency of the injection moulding. Such cooling channels are not possible with traditional techniques. A second advantage is that a 3D-printed mold can be combined with Rapid Heat Cycle Technology. You can use this to produce beautiful high-gloss injection molded products.”
According to him, the major advantage of the innovation cluster is synergy. “3D printing offers new opportunities. One company has a high level of knowledge of finishing techniques, while another company has a strong competence in metallography. The combination of these competencies and resources creates value for all parties in the project. You learn from each other in the innovation cluster. In addition, we share investments and also support each other with the use of certain equipment. For example, we make our electron microscope available for research into the surface of 3D-printed metal. And it's also just fun to work with other high-tech companies in the area!”