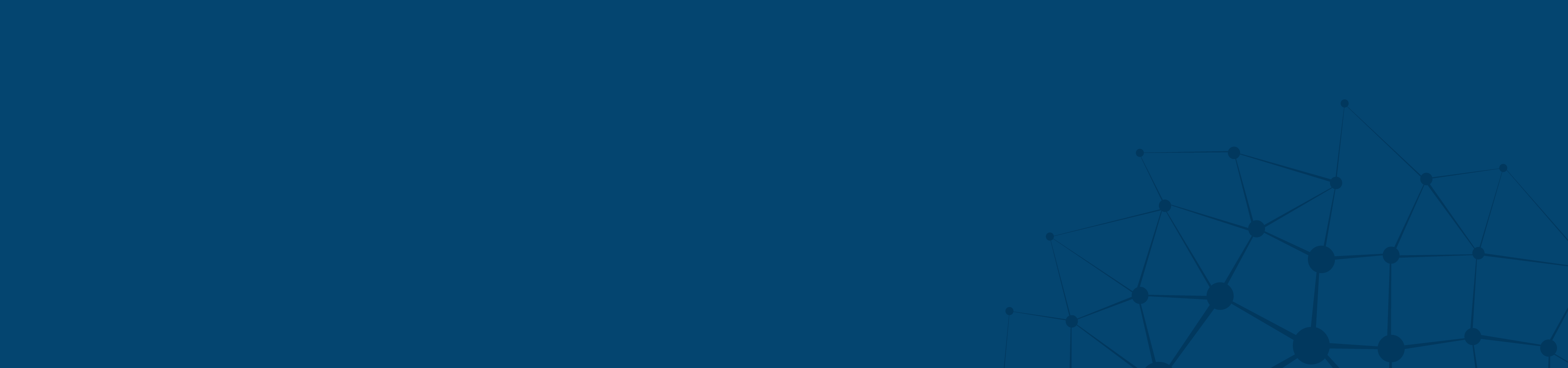
ICD Learning Day: Human is the ultimate flexible machine
News | December 5, 2019

The Philips auditorium in Drachten is buzzing like a kind of indoor fair during the annual ICD Learning Day. Employees of the Innovatiecluster Drachten companies view and discuss the results of their own R&D projects. For a year they 'tinkered' with technical challenges and today they show their findings. To each other, because sometimes it concerns innovations that make a competitor jealous.
'I haven't failed. I've just found 10,000 ways that won't work. The suggestion in this statement by Thomas Edison that making many mistakes is necessary to innovate is not shared by program manager Joost Krebbekx. Innovating is organizing as much as possible by chance, he explains to almost a hundred participants in the ICD Learning Day in his introduction to the program. That is exactly what is happening at Philips in Drachten on Thursday 28 November. Techies from 21 high-tech companies from the Northern Netherlands taste each other's kidneys. With short pitches about their projects and feedback during the 'free flow'.
paperless
"Hey Ben, nice to have you back. You were last here four weeks ago. There are some changes in the hydraulic arm assembly. Some parts have to be constructed differently. I'll show you how to do this.” Ben Scholtanus, operations manager at Neopost, paints a picture of a 'paperless factory'. ,,This happens when I log on to the production line after my vacation. The system keeps track of what I did last time and thus gives the right feedback to get to work. In this way I never miss a transfer from a colleague and I am also not surprised by new parts in the tank.” Together with R&D managers from Variass, Norma, Ventura Systems and Photonis, Ben is working on a solution to the question: how you get the right information about a product, at the right time with the right people. This is about much more than work instructions on a screen. It is about connecting all available data of a product, which results in a complete picture from design process to production process to the use of the end product.
More than instructions
Ben gives an example. ,,With our inserting machines, customers collect documents, which are folded, put in an envelope and receive an address sticker with barcode. Sensors in the device monitor critical parts for wear and also signal failures and errors. Linked to the internet, this information comes to us.” According to Ben, the challenge is to get the right information about errors and wear from the product designers, so that they can take it into account for a new version. “After that, designers have to put the changed design into a new assembly schedule, after which buyers have to know which new parts to order. Finally, the changes about new parts or the order of assembly must reach employees on the production line. And all of this preferably as quickly as possible, in order to improve the product and keep costs as low as possible.” Ben is convinced that the 'paperless factory' not only increases the quality of the product, but also the time to market decreases. “The pace of changes to your products is increasing and so is the quality of your data. Employees build on experience and no longer look to instructions. In the 'paperless factory', in addition to instructions, employees immediately receive an explanation of why and how. This means you will never do the same thing again for 20 years.”
Flexible production
Not only processes become better and smarter in a smart factory, machines also undergo a metamorphosis. They are connected and read out with each other and the internet, for a good picture of what really happens in the factory. Processes are optimized, lead times are shortened and work is done more efficiently. Jan Jacob Mosselaar, system architect at FMI, is working on a 'multidisciplinary architecture' to enable flexible production. His challenge? Giving flexible machines human characteristics. For example, responding to sudden events, self-learning ability and assessing situations. In fact, humans are the ultimate flexible machine, so let's take a good look at ourselves."
blocks
A robotic arm with a gripper grabs products of different sizes and places them on another product. The actions seem arbitrary, but nothing could be further from the truth. The arm works accurately and reliably. There is no doubt about the size or placement of the product. Jacob explains. “Robots need to know what to grab, so we fill it with parameters from outside. That way it becomes flexible.” Yet you cannot go on indefinitely with making a robot flexible. Moreover, not all variables are always known in advance. That is why we work with so-called 'building blocks'. “You automate these blocks and only then do you make them more flexible by using them alternately. The advantage is that you can use blocks from previous machines. It is also possible to build separate units, each with its own standard, which are interchangeable and usable in different machines.'' Whether flexibilization can continue indefinitely? “No, there is a limit somewhere. Making machines flexible is expensive. In addition, it is often more practical to have multiple machines that perform specific tasks. You never need all the functions at once."
Overview ICD R&D projects
- Smart Machines 2.0
Predictive maintenance and quality control in remote high-tech systems based on big data/clouds
- Component & Parts inspection by Vision
New combinations of new vision cameras and light to inspect objects automatically
- AI & Machine Learning
The way to achieve information out of multiple databases
- Connected Collaborative Robots 2.0
Robots and cobots for different manufacturing processes, connected to MES
- Paperless factories
The first step to digital twinning on the production floor
- Advanced Additive
New metal 3D printing applications, production-speed printing of engineering plastics, and the 3D printing of electronics
- flexible machines
Defining a multi-disciplinary architecture to enable flexible manufacturing
- Environmentally Protected Electronics
Improving reliability of electronics under harsh conditions.