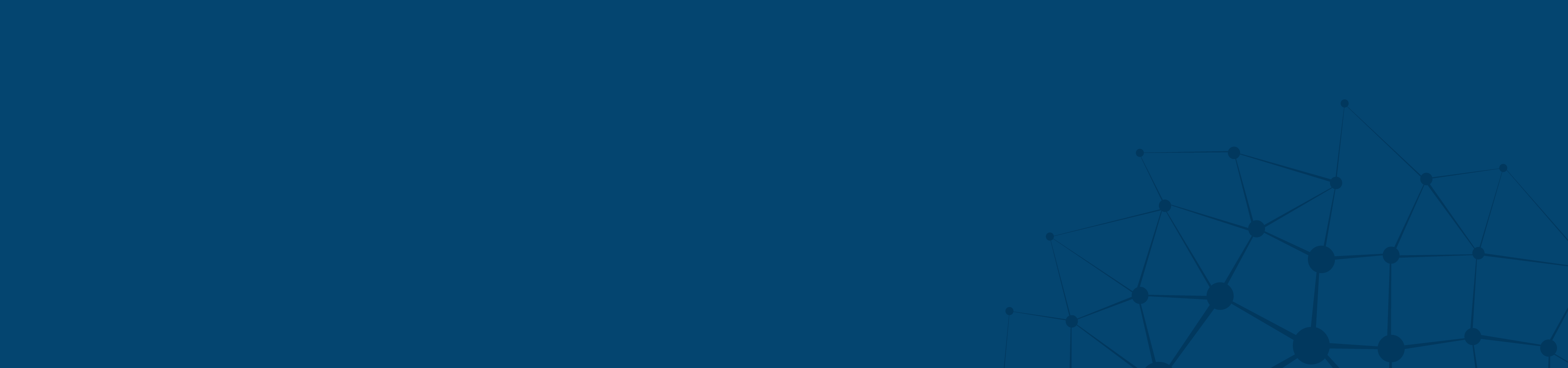
Variass is reaping the benefits of investments in cobots and data integration.
In the media | 15 Jul 2021
By collaborating with Innovatiecluster Drachten, we have been able to implement product quality and process improvements through innovation within the R&D projects.
It started a few years ago with VERA – Variass First Robot Arm. In addition to a soldering cobot, other solutions have now been developed for trading, testing and connection techniques, namely cobots that 'pack, screw, glue, test and repair. 'We have converted many manual tasks into cobots with a view to sustainable employability of employees. If you remove relatively simple or repetitive actions, it takes the position of employees to a higher level', says director Henk Smid. 'You don't need a technical employee to apply sixty screws in line, a cobot can provide excellent support there. The ultimate goal is to improve product quality and the process. Where humans might forget to tighten a screw, the cobot won't skip one.'
Cobots also help to solve another problem: the scarcity of technical personnel. And as soon as employees overcome their initial fear that they will lose their job due to robots and cobots, there is also a bit of social innovation. 'Employees see that their job is becoming more professional and that we are bringing in extra work by automating tasks', says Smid. Thanks to the cooperation between robot arm and employee, work processes run faster and this shortens the lead time of the production process. 'That way you can achieve growth with your existing people', says Smid. 'Plus lower your cost. This persuades customers to do more with us instead of possibly moving to low-wage regions. That way the investment pays for itself.'

That costs Variass about € 50,000 per cobot for a certain application, so a few hundred thousand at the front, with the payback time varying between two and four years. 'There is already an advantage if the cobot carries out repetitive work from 50 units, explains Smid. 'We want to maintain the lead we have with such innovations.'
The same goes for the data integration platform that Variass developed and implemented in collaboration with spin-off Arkoni. Where the cobots physically support the employees on the production floor, the data integration platform does that by indirectly automating simple tasks and offering decision support for more complex tasks. 'Cobotization, 3D printing, digital production. Now that information is digitally available much faster, you can implement improvements faster, all of which contributes to de-optimization (??).' Not only Variass itself, but also customers benefit from this. 'During developments, we can take into account how a product is produced and work in parallel with a digital twin. By improving both the quality and the process, a better product is created at a lower cost. That has been standard at SMT for a long time, we can develop it even further with cobotisation.'
The original article can be read at LinkMagazine